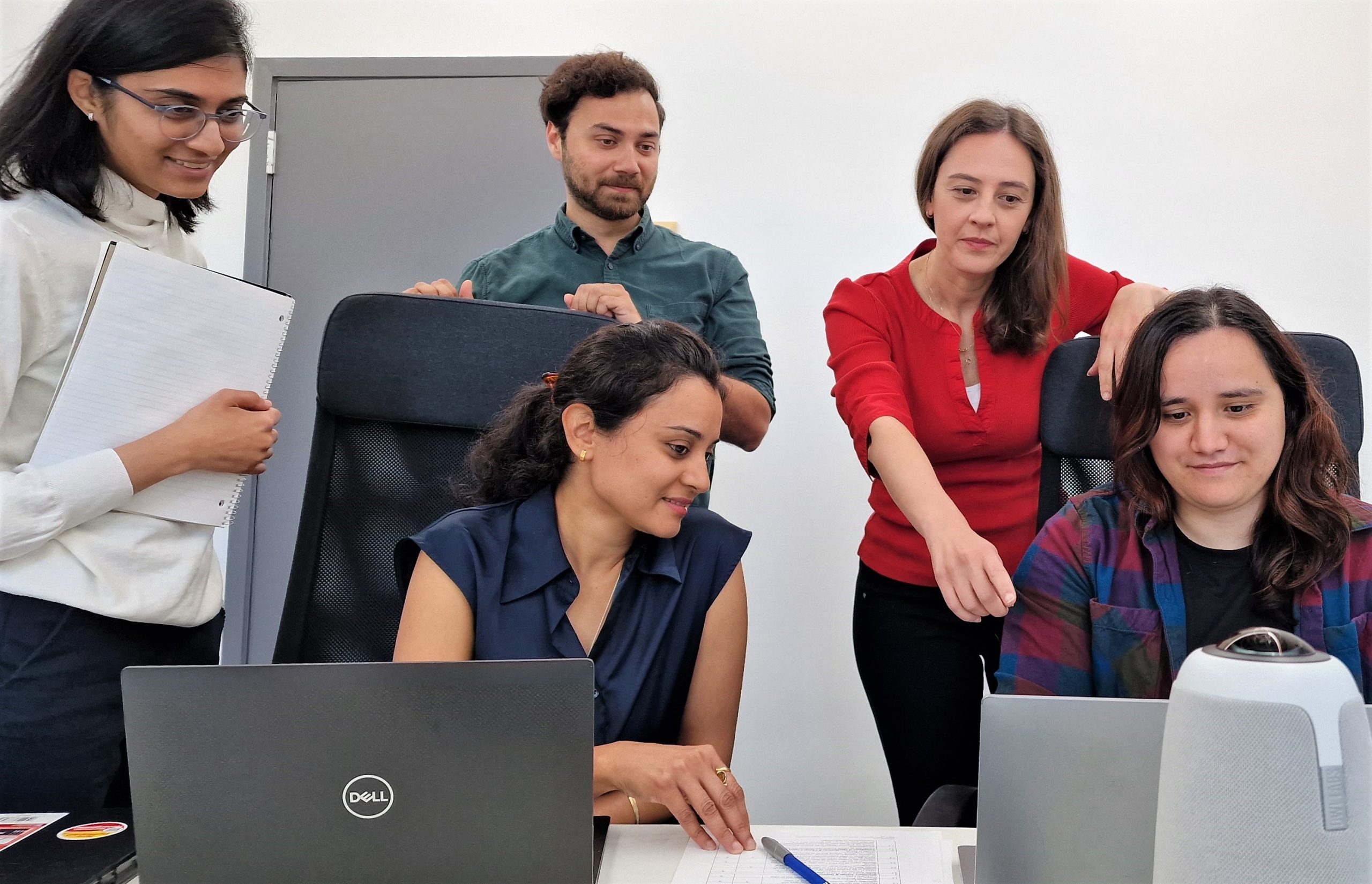
As you gear up to face your impending FDA inspection, we’re here to lend a helping hand with five crucial tips for a smooth and successful FDA inspection.
Navigating the intricacies of regulatory compliance can be daunting, but fear not! Our expert advice will guide you through this difficult process, so your organization is well prepared to meet the FDA’s requirements.
Tip #1: Live notes and inspection space setup
Controlling the flow of information and people are key to a successful inspection and should be a major part of your Game Plan. The first tip is on setting up the inspection space and establishing roles and responsibilities for the host team. This involves having a front room and back room with team members assigned to each room who understand exactly what they are responsible for.
The Front room should be a calm and controlled space. It includes the inspector(s), one or two QA/RA staff, a runner, and a scribe. Subject Matter Experts (SMEs) should be brought in to field questions as needed. QA/RA hosts the inspection and takes care of general quality related queries in the front room. The scribe takes notes in a shared document, which is available LIVE to the back room so that the full team is aware of where the audit is heading and can prepare supporting documents. There should also be an active, online chat set up to communicate requests. The runner acts as a communication bridge between the front room and the back room, providing the right document at the right time.
The Back room, also known as the war room, is where the behind the scene interactions take place between another set of QA/RAs and the SMEs. In the back room, QA/RAs review documentation before it leaves the room and keep a record of all the requests and documents provided to the inspector. The back room is a good place to keep SMEs on standby and to help them get up to speed on the inspection prior to entering the front room.
Tip #2: Read the QSIT guidance
What is 108 pages long, from August 1999 and a gem of a resource when preparing for an FDA inspection? If you guessed the FDA’s Guide to Inspections of Quality System, you are correct. This document was published as a guide to FDA field staff on a then ‘new’ inspection process referred to as QSIT (Quality System Inspection Technique). It is divided into four main sections that when taken together provide inspection coverage for 21 CFR 820 (Quality System Regulations), parts of 21 CFR 806 (Recalls, Corrections and Removals) and other medical device regulations.
The four sections are Management Controls, Design Controls, CAPA and Production & Process Controls. The guidance provides the inspector with an approach that maximizes their effort in focusing on areas of interest such as processes that result in CAPAs and complaints. By understanding the four areas of interest within QSIT your organization can focus efforts on preparing documentation and narratives that are covered within. This will allow for a more seamless inspection and will prevent the inspector waiting while items like CAPA lists and redacted management reviews are prepared.
Tip #3: Know the project history
When facing the prospect of an FDA inspection, it is important to set some time to look back into the history of changes, non-conformances, and field issues. This exercise provides a space for the team to identify, analyze and prioritize preparation efforts/resources leading up to the inspection. It familiarizes the team with the most relevant areas that have impacted manufacturing and/or design and increases the confidence of the team when faced with questions surrounding these topics during the inspection.
There is a story and reason for everything that has happened and it’s important to gain understanding within the full team and present an accurate and consistent narrative to the inspector.
Tip #4: Mock inspection / internal audit
Conducting a Mock FDA inspection can significantly enhance your organization’s readiness. Timing of this activity is easier when the inspection is scheduled, as is the case for foreign inspections.
Mock audits can be a rehearsal for the actual inspection. They can involve bringing in experienced auditors, either from within your organization or external consultants, who can simulate an FDA inspection. Here’s why they are helpful:
- Identify Gaps: the mock auditors can assess your operations, documentation, and processes against FDA regulations. This helps identify potential gaps or weaknesses in your system. This is especially useful if the auditors are individuals who are external to your organization or far removed from the program as they are more likely able to look at your process without bias.
- Corrective Actions: Issues detected during a mock audit give your team an opportunity to address them promptly. This proactive approach allows you to implement or document corrective actions before the FDA arrives. Corrective actions do not necessarily need to be implemented in full, but it is helpful to demonstrate that they have been identified and are in progress.
- Train and Familiarize Staff: Mock audits provide valuable training for employees who are not involved in inspections on a regular basis. They can get an idea of what to expect during the actual inspection, reduce their anxiety and increase their preparedness so they can answer questions appropriately.
- Assessment Readiness: A mock audit can help gauge your organization’s readiness for the real FDA inspection. It might seem difficult but serves as a reality check, enabling you to assess corrective actions, update procedures and prepare appropriate documentation.
Tip #5: General preparation tip
This tip discusses general preparation aspects that should be kept in mind before and during the inspection. Some may sound trivial, but will help avoid awkward pauses and frantic responses, to what should be seamless interactions.
To begin with, have a sign-in sheet ready with the names and titles of attendees. Also request the FDA inspector to sign it and ensure that the sign-in sheet is a controlled document. Before beginning the inspection, politely ask the FDA inspector for their badge and make sure to check it (without touching it). Do not forget to ask for form 482 – Notice of Inspection.
When beginning the inspection, a PowerPoint presentation explaining the general workflow of the product and an overview of the company is generally expected as an introduction. It is also good practice to have all the employees know the company’s ‘Quality Policy’ in case the inspector happens to ask.
Be sure to control what information is displayed on softboards of the company, as the inspector might ask questions while they take a tour of the facility. Furthermore, if there is material lying in the manufacturing area that is out of scope for the given inspection, ensure it is adequately labeled to avoid unwanted attention from the inspector. Lastly, be comfortable with silences and do not feel the need to fill them.
Conclusion
Whether you are given advance notice as part of an international inspection or have the FDA knocking on the door unannounced, it pays to prepare. This preparation is a combination of awareness of what the inspector is looking for, understanding the history of your product and where potential issues lie, and evidence to demonstrate that you are working towards correcting those potential issues.
Additionally, having a solid game plan for the logistics of the inspection will give you an extra edge. When the big day finally arrives you will be calm, confident and able to flash the inspector a big shiny smile as you dive right into demonstrating that your product and organization meet the regulations and things are under control. You and your team have got this!
Image: StarFish Medical
Deborah Pinchev is StarFish Medical’s Toronto QA/RA Manager. She is inspired to write blogs by her interest in helping companies develop and bring to market new and innovative devices.
Taimoor Khan is a QA/RA Specialist at StarFish Medical. Based in our Toronto office, Taimoor works on a variety of medical device projects. He follows his own advice on ROHS and REACH management and qualification regularly.
Maria Gonzalez is part of the QA/RA Team at StarFish Medical. She likes analyzing the procedures needed to bring medical devices to market and adapting them to the manufacturer’s current needs and expectations.
Vinky Kohli is a QA/RA Specialist in StarFish Medical. Vinky has done her Master of Engineering in Biotechnology and has experience in Pharma and medical device industries in QA/RA, product development, QMS development and maintenance. Vinky has passion for quality work including documentation.
As a member of the QA/RA team, Bhavyashree is dedicated to ensuring product quality and compliance. With a keen eye for detail, she strives for excellence within the field of quality assurance and regulatory affairs.