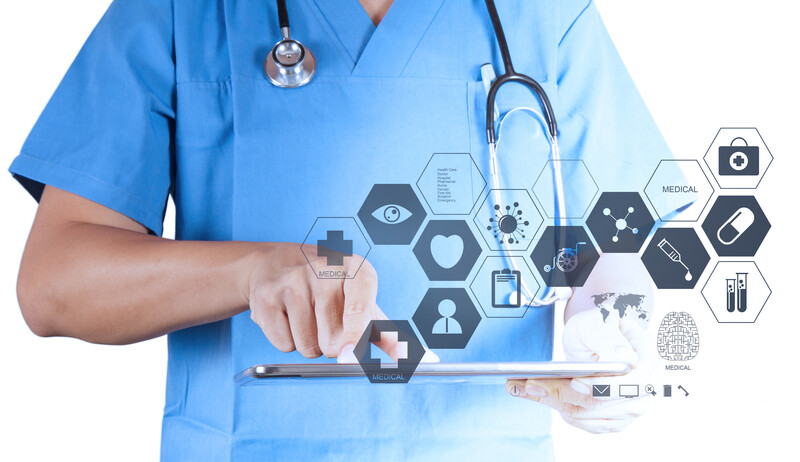
The FDA requires a UDI in both plain text and machine-readable format (i.e., bar code) to be printed on a label that is attached to the device and the device packaging for traceability through distribution and service life of the device.
With the UDI being generated at the time of manufacture, it is much more cost- and time-efficient for medical device manufacturers/labelers to print the labels in-house rather than procuring the labels from a label vendor.
However, if the UDI labels are printed in-house, how can medical device manufacturers/labelers verify that the printed labels meet the labeling requirements and standards? How can medical device manufacturers/labelers know objectively that UDI labels are durable and readable by both humans and machines so that medical devices remain identifiable and traceable over its service life?
These questions lead us to the importance of UDI label verification:
Verifying UDI Labels
Aside from visually ensuring that all of the required information is present and accurate on the printed label, the most important verification step is to verify the machine-readable UDI (i.e., barcode) print is of sufficient quality to ensure that it is universally readable.
A common misconception is that scanning the UDI code with a barcode scanner can be used as a verification method, but this is not true since the barcode scanner only reads the code so there is no guarantee that a successful scan with one barcode scanner equals successful scans with others. Therefore, to properly verify the machine-readable UDI, a barcode verifier is required.
A barcode verifier is a regularly calibrated device to ISO/IEC 15426-1 (1D) or ISO/IEC 15426-2 (2D) that works like a scanner and has the capability to objectively grade (alphabetic or numeric) the overall quality of the machine-readable UDI to ISO/IEC 15416 (1D) and ISO/IEC 15415 (2D) standards and generate a comprehensive report. Some of the barcode attributes it can measure are edge determination, decode, minimum reflectance, symbol contrast, minimum edge contrast, modulation, defects, decodability and minimum quiet zone, as well as identify issues such as incorrect UDI formatting, poor print resolution, and undersize UDI code.
There are also vendors that offer barcode compliance testing, print quality testing, and barcode consulting with these barcode verifiers and can perform this barcode verification for device manufacturers/labelers. Currently, there is no regulatory requirement to perform 100% verification on UDI codes, but periodic verification is highly recommended to ensure the printing process is controlled.
Figure 1: Sample UDI label verification report
Definitions:
Scan Reflectance Profile – A map of the localized symbol reflectivity as a measuring aperture is scanned across the symbol along a specific path. The peaks of the profile illustrate the largest value of reflectance (the barcode’s spaces) and the valleys of the profile indicate the smallest value of reflectance (the bar code’s bars).
Data Format Check
HIBC Data Flag – A fixed character “+”.
Labeler ID Code – A 4-character code that is controlled by the Health Industry Business Communications Council (HIBCC).
Product/Catalog Number – A 1-to-18-character alphanumeric number assigned by the labeler to identify item/device.
Unit of Measure ID – A numeric value assigned by the labeler to identify the packaging configuration level of the item e.g., carton, case, pallet, unit, etc.
Data Delimiter Character – A character that separates the primary and secondary data.
Date Format Flag – A numeric value that defines the date format used.
Lot/Batch – Lot/batch number.
DI: Prod. Date – Date of manufacture.
Prod. Date – Date of manufacture.
Check Character – Character added to prevent undetected errors.
General Characteristics
BWG – Bar width growth is a measure of ink spread.
Nominal X Dimension – The width of the smallest bar in the barcode. This also determines the smallest barcode size.
ANSI/ISO Parameter Values
EDGE – Refers to how the scanner’s laser perceives the edge of the barcode (where the lines end and the spaces begin).
Reflectance Light/Reflectance Dark – This indicates how distinguishable the elements of the symbol are. A poor reflectance margin may result in an element being incorrectly designated as dark or light.
Symbol Contrast – A measure of the contrast between the brightest space on the barcode and the darkest bar.
Minimum Edge Contrast – Measures the contrast between adjacent bars and spaces.
Modulation – A measure of the local variations in contrast.
Defect – The most apparent change in darkness within a bar or space.
Decode – This refers to the ability of the scanner to decode the information present on the barcode based on the sequence of the bars and spaces.
Decodability – Measures how close the scan reflectance profile is to failing the “decode” parameter.
Minimum Quiet Zone – The minimum amount of space to the left and right of the barcode.
Ensuring Label Durability
In addition to verifying the UDI code, it is also important to verify the label durability to ensure that the label remains clearly legible during the expected service life of the device. For reference, this requirement is specified in Medical Electrical Equipment IEC 60601-1 Part 1: General requirements for basic safety and essential performance subclause 7.1.3 Durability of Markings.
Basic verification includes a rubbing test performed with distilled water, methylated spirits ethanol 96 % (C2H6O), and isopropyl alcohol (C3H8O) for 15 seconds to ensure the print does not smear/fade and the label does not curl, peel, or fall off. If the medical device is designed to be exposed to other harsh chemicals, additional tests will be required with those chemicals to ensure compatibility.
In addition to the rub test, UDI labels are also tested for UV fading. This test is performed simply by exposing the label to UV light for an extended period to see if fading occurs. The most important considerations to improve verification success rate of label durability are the printer type and label material.
There are four generic types of label printers (thermal transfer, direct thermal, inkjet, and laser printer) and two categories of label material (paper and synthetic) on the market. Each printer type and label material have its advantages and disadvantages, but the most durable printer type and label material combo for UDI labels is thermal transfer paired with synthetic labels and ribbons because it’s most resilient to the above verification methods.
The most important aspect to consider for selecting the right label material/printer type to guarantee successful label verification is clearly defining and understanding what the UDI labeling requirements for the device are.
Simple Steps to Ensure Robust and Compliant Medical Device Labels
By performing and passing the above UDI label verification tests, medical device manufacturers/ device labelers can be confident that their UDI labels meet industry standards and eliminate the risk of losing identification and traceability on their devices.
Image: StarFish Medical
Eddie Yeung, is a StarFish Medical Mechanical Engineer.