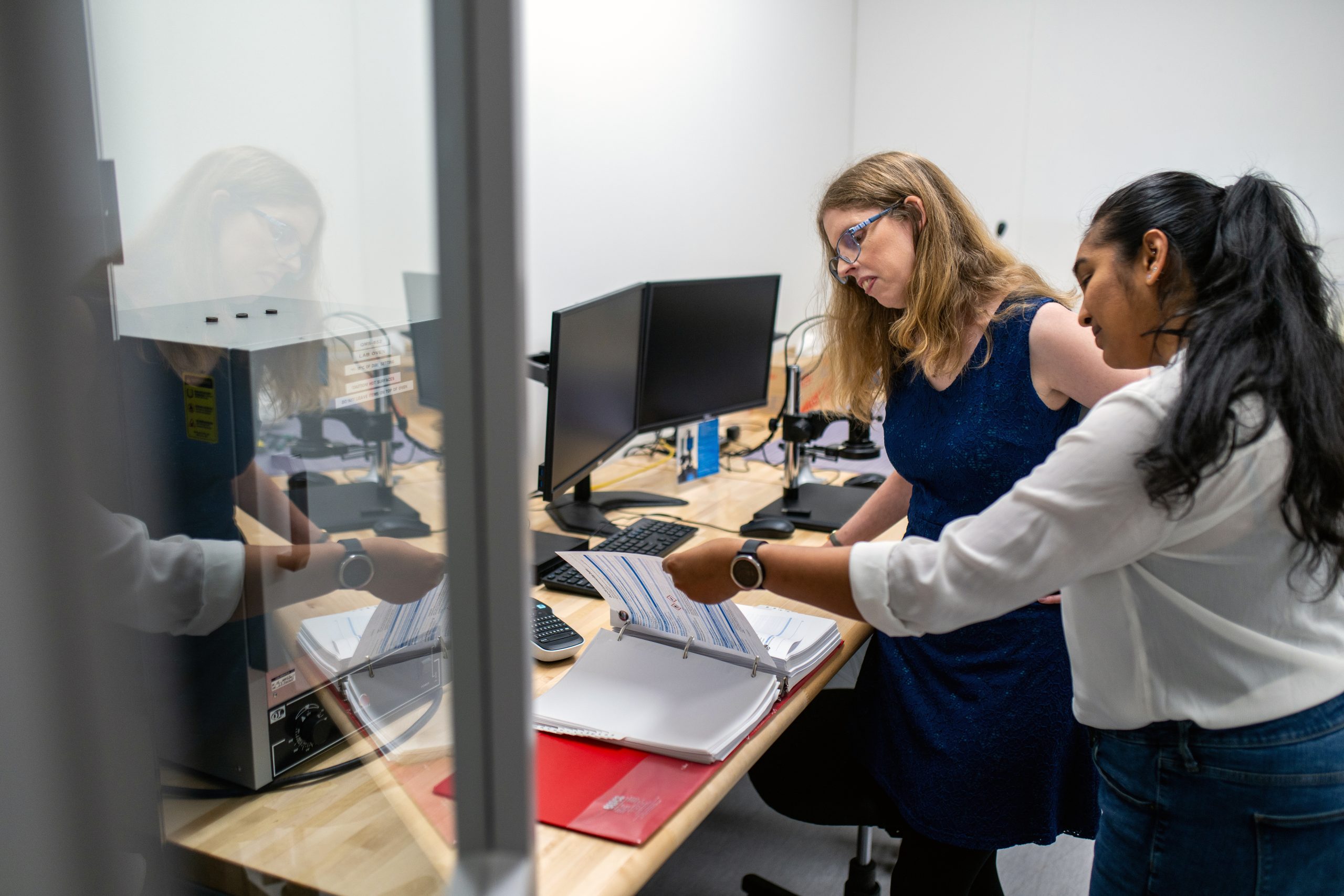
When thinking about the roles of Quality Assurance (QA) and Regulatory Affairs (RA), I like to use the metaphor of the trail blazer and the guide, RA is there to blaze the trail and find the path, QA is there to keep the team on that path and away from pitfalls and hazards.
RA does this by monitoring and reviewing the regulatory landscape, understanding the applicable laws and regulations, but also knowing about recent decisions by regulatory bodies and how interpretations of these directives and guidances can vary. QA keeps projects on track by being fully engaged in the Quality Management System (QMS) and knowing what needs to be done to ensure that the project is successful as well as compliant.
In this way the QA/RA team help and support the Product Development and Manufacturing teams to bring successful innovative products to market.
How does QA/RA provide value to a medical device project?
Embarking on developing a new product
When embarking on a new product development, the opportunity to explore is wide open. For some people this is positively embraced, for others it can be daunting. This is where a well-informed regulatory specialist can help navigate how to approach the project and identify where you want to take it. Regulatory teams can advise on the ease or difficulty of different regulatory pathways, which are more direct, which are more long-winded, and how this interacts with the business strategy.
Once regulatory specialists have helped plan your regulatory strategy, QA can work with the team to put in place the structure to help realize that.
On-going development
Throughout the development, QA keeps the project on track to the vision laid out in the regulatory strategy by advising the team on appropriate actions to take, reviewing documentation to ensure completeness, accuracy, and traceability, and maintaining an ISO 13485 / QSR compliant QMS to work within. QA/RA team members use their knowledge of the regulatory and quality requirements to help the team and clients find solutions to challenges within the project. This ensures the project runs smoothly, remains compliant, and supports a regulatory submission at the appropriate time.
Transfer to manufacture
When a product is ready for transfer to manufacturing, the QA/RA team works with the project team to support that transition and create manufacturing documentation that aligns with the design documentation and supports the regulatory requirements for that product. This ensures that the manufacturing process supports successful manufacture of product and generation of appropriate records which allows the release of safe and effective products.
Regulatory approvals
Regulatory approval is the part of getting a product to market when the QA/RA team become the lead players in the project.
QA/RA team members analyze the documentation generated during the development and compile the necessary information into a format ready to be submitted for the relevant approvals that were laid out in the regulatory strategy. Depending on which regulatory pathway the product is taking, this may also include supporting audits or inspections, and providing manufacturing documentation and evidence of compliance.
Once the submission goes to the relevant regulatory body, the regulatory specialists work as a liaison between that regulatory body and the project team and clients to get requests for additional information or queries answered as quickly as possible to keep the approval process moving forward efficiently.
Routine manufacturing
Once a product is transferred and moves into more routine manufacturing, the primary task for QA is product releases. Here QA are the final check and balance to ensure that products are fit for purpose and safe for users before they go out of the door. Whilst this is a regulatory requirement, QA also see it as their obligation to ensure that only the best products are shipped to maintain our client’s reputation.
QA/RA team members also provide support to sustaining engineering teams, ensuring that changes to the product are carried out appropriately, and that the regulatory approvals are considered during this process. They work closely with internal and external clients providing significant change assessments and regulatory advisement when amendments to approvals are required.
Where appropriate, QA/RA can also support post-market surveillance activities, collating data about the product(s) and carrying out data analytics to advise on appropriate action plans. Our QA/RA team routinely provides trending data on all our product monitoring for key clients.
Conclusion
Here at StarFish Medical, we choose to have a combined Quality Assurance (QA) and Regulatory Affairs (RA) team. Working on projects with our internal and external clients, we provide consistent support throughout the lifecycle of the project from a team member who is familiar with the context of the project from both perspectives.
Being in QA/RA gives a great overview of the end-to-end lifecycle of products. Working in a consultancy like StarFish Medical allows us to experience a wide range of products across medical device, IVD and lab equipment industries, which gives us perspective on a wide range of challenges.
I hope you found this article useful and look forward to hearing from readers to you and how we can help you navigate the challenges present in any product development and find you a successful path to market.
Image: StarFish Medical
Helen Simons is a Director of QA/RA at StarFish Medical. Helen’s education is in Mechanical engineering, with a background of product development and QMS development across multiple industries with consumer and industrial products to medical devices, IVD and combination devices.